Discover the Benefits of Various Kinds Of Welding Providers for Your Organization

In the world of industrial procedures, the choice of welding solutions plays a critical duty in figuring out the quality and effectiveness of your business procedures. Each welding strategy, from MIG to TIG, Arc, and Area welding, offers distinctive advantages that cater to details requirements and needs.
MIG Welding Advantages
MIG welding, likewise referred to as Gas Metal Arc Welding (GMAW), provides countless advantages to businesses seeking high-grade and efficient welding services. One key advantage of MIG welding is its adaptability in taking care of various types of steels, consisting of stainless-steel, aluminum, and mild steel. This versatility makes MIG welding a preferred choice for industries with diverse welding requirements.
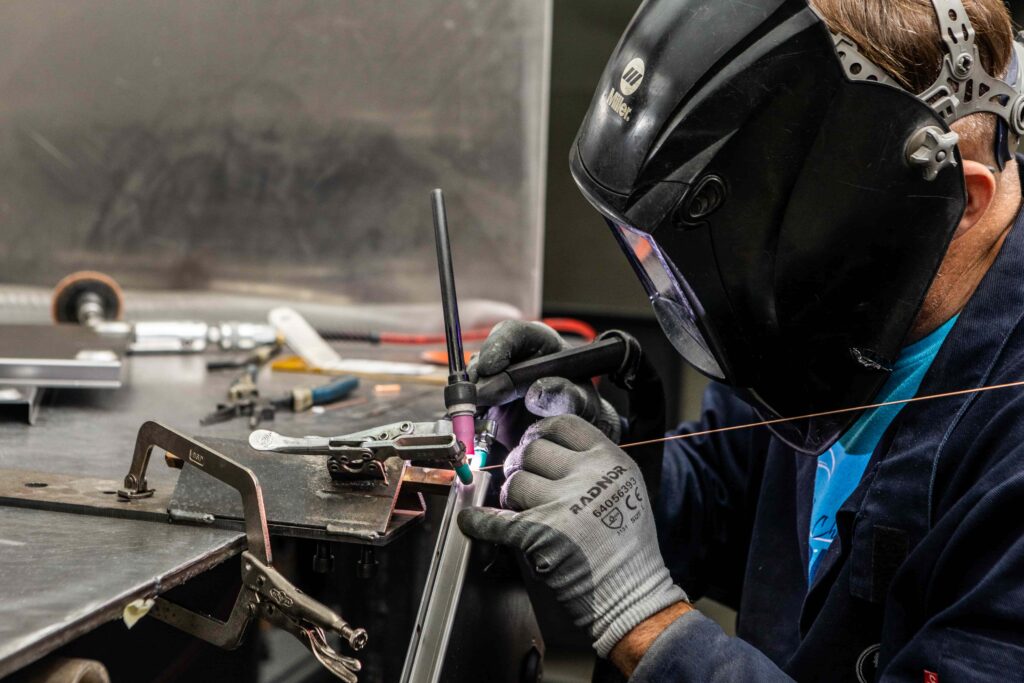
In addition, MIG welding is an economical option because of its efficient usage of consumables such as filler material and shielding gas. This efficiency equates to savings for organizations in the long run. On the whole, MIG welding's combination of adaptability, rate, ease of usage, and cost-effectiveness makes it a preferred option for several welding applications.
TIG Welding Advantages
Tungsten Inert Gas (TIG) welding uses precise control and outstanding quality in welding solutions for organizations requiring precise and high-standard welds - Welding Inspection Service. TIG welding stands apart for its capability to generate clean and accurate welds without spatter or triggers, making it perfect for applications where appearances and precision are critical. One of the crucial benefits of TIG welding is its versatility in welding different types of metals, including stainless-steel, light weight aluminum, copper, and unique steels, providing companies with a versatile welding option for different tasks
Additionally, TIG welding makes it possible for welders to deal with thinner materials effectively, as the process enables lower heat input and better control over the welding arc. This leads to very little distortion and a narrow heat-affected zone, vital for welding jobs where protecting the architectural stability of the base materials is important. Furthermore, TIG welding creates high-quality, visually appealing welds that often require very little post-weld cleaning, conserving services time and resources. In general, the accurate control, premium welds, and flexibility make TIG welding a favored choice for businesses looking to attain excellent welding outcomes.
Arc Welding Pros

Spot Welding Perks
Place welding uses numerous advantages for organizations seeking exact and reliable joining of steel parts in their manufacturing procedures. This welding approach is highly economical due to its quick implementation, marginal need for substantial prep work, and lower power consumption contrasted to various other welding techniques (Welding Inspection Service). Spot welding likewise gives a clean and neat coating, making it optimal for applications where aesthetics are vital
Among the vital benefits of spot welding is its capability to produce solid and sturdy bonds in between steel surface areas. The procedure creates a focused warmth resource, resulting in a localized weld that reduces damage to the bordering locations. This concentrated warmth application additionally reduces the risk of warping or distortion in the welded products, ensuring the integrity of the end product.
Additionally, area welding is extremely flexible and can be utilized on a vast array of metals and alloys, consisting of steel, copper, and aluminum. Its versatility makes it a prominent choice for industries such as automotive, electronics, and aerospace, where accuracy and browse this site effectiveness are paramount. In general, the benefits of spot welding make it a valuable property for services click this seeking to improve their manufacturing capacities.
Welding Solution Selection Factors
One more element to consider is the dimension and intricacy of the elements being welded. Some welding approaches are much better suited for small-scale and detailed tasks, while others are a lot more effective for larger and more uncomplicated frameworks. Think about the speed and performance of the welding procedure. Depending on your manufacturing demands, selecting a welding solution that can fulfill your timeline and outcome needs is essential for maintaining productivity. Assess the cost-effectiveness of various welding services to make certain that you are getting the ideal value for your financial investment. By meticulously thinking about these aspects, you can choose one of the most suitable welding solution for your business demands.
Final Thought
To conclude, comprehending the advantages of various sorts of welding solutions can article substantially profit organizations in their decision-making process. MIG welding offers efficiency and speed, TIG welding offers high precision and clean welds, arc welding is flexible and economical, and place welding is ideal for joining thin materials. By thinking about these aspects, services can choose the most appropriate welding service to meet their particular needs and requirements.
MIG welding, also known as Gas Steel Arc Welding (GMAW), uses many benefits to companies seeking efficient and high-quality welding solutions. One of the crucial advantages of TIG welding is its flexibility in welding different kinds of metals, including stainless steel, light weight aluminum, copper, and unique metals, providing organizations with an adaptable welding option for various tasks.
Arc welding is recognized for its high welding speed, enabling reliable completion of welding tasks (Welding Inspection Service). On the whole, the pros of arc welding make it an important welding service for organizations looking for a flexible, affordable, and efficient welding option
MIG welding provides performance and speed, TIG welding provides high accuracy and tidy welds, arc welding is cost-efficient and flexible, and place welding is suitable for joining slim materials.